Скачать книгу из которой взят данный материал
Гл. 1, п. п. 2.2—2.4, 3.1—3.4, 3.6 написаны Р. А. Коротковым, п. п. 2.1, 3.5 и 3.7 — Ю. Ф. Игнатенко, гл. 4 — М. Б. Беккером, гл. 5, 8 и 9 — М. Л. Заславским, гл. 6 и 7 — В. Я. Невзоровым.
СОВРЕМЕННЫЙ УРОВЕНЬ И ОБЛАСТИ ПРИМЕНЕНИЯ ЛИТЬЯ ПОД ДАВЛЕНИЕМ
1.1. ЭТАПЫ РАЗВИТИЯ ПРОЦЕССА
При литье под давлением металлический сплав в жидком или твердожидком состоянии подается в камеру прессования специальной машины под давлением, создаваемым перемещающимся в этой камере поршнем, с высокой скоростью через литниковые каналы заполняет полость пресс-формы и затвердевает в ней под давлением. При раскрытии пресс-формы отливка извлекается.
Существуют четыре основные схемы процесса литья под давлением, позволяющие получать широкую номенклатуру отливок из различных сплавов.
Первая схема — литье под давлением на машинах с горячей камерой прессования (рис. 1.1). Камера прессования заполняется металлом из тигля 4 через заливное отверстие 3. Расплавленный металл под давлением поршня 1, приводимого в движение пневматическим или гидравлическим цилиндром, вытесняется из камеры прессования 2 в полость пресс-формы 5 при перекрытом отверстии 6. Металл затвердевает, образуя отливку 7, а прессующий поршень возвращается в исходное положение. Незатвердевшая часть металла сливается по каналу мундштука 8 и металло-проводу 9 в камеру прессования. После охлаждения до заданной температуры отливка удаляется из /рабочей полости формы. Пресс-форма очищается, смазываете^, и рабочий цикл повторяется.
Технологическими преимуществами этой схемы является стабильность технологических параметров, отсутствие потерь сплава в процессе заливки, широкие возможности автоматизации всего литейного цикла, высокая производительность. Существенные недостатки — быстрое изнашивание прессующей пары (поршня и камеры прессования), образование зазора между ними, что приводит к снижению давления прессования. Это вызывает повышенную пористость, снижение качества поверхности, четкости оформления конфигурации отливки.
Литьем под давлением на машинах с горячей камерой прессования можно получать отливки из сплавов не реагирующих с материалом прессующей пары и металлопровода.
Вторая схема — литье на машинах с холодной вертикальной камерой прессования (рис. 1.2). Расплавленный металл заливается в камеру прессования 1 с подвижным дном 2, называемым
Рис. 1.1. Схема литья под давлением иа машинах с горячей камерой прессовании
пяткой. Прессующий поршень 3 в момент заполнения камеры находится в верхнем положении, затем он опускается на металл, перемещая пятку вниз и открывая отверстие в литниковой втулке 4, через которое металл поступает в полость формы 5. После затвердевания Металла пятка поднимается, отделяя литник от пресс-остатка 6. После раскрытия пресс-формы выталкивателями из ее подвижной части удаляется отливка 7 вместе с литниковой системой.
Технологическую схему с вертикальной камерой прессования целесообразно применять в тех случаях, когда отливки имеют глубокие полости при относительно небольшом ходе подвижной плиты машины на раскрытие, когда нужно использовать центральный литник. При литье по этой схеме неметаллические включения, имеющиеся в расплаве, задерживаются в пресс-остатке, так как площадь литника значительно меньше площади камеры прессования.
Третья схема — литье на машинах с холодной горизонтальной камерой прессования (рис. 1.3). Расплавленный металл заливается в камеру прессования 2, расположенную горизонтально по оси машины и перпендикулярно к плоскости разъема формы, непосредственно связанную с неподвижной половиной формы 1. В верхней части камеры имеется окно 3 для заливки металла. При движении пресс-поршня 5 металл через питатель 4 заполняет рабочую полость формы. После окончания кристаллизации металла форма раскрывается, и отливка 6 с пресс-остатком 7 выталкивается пресс-поршнем из неподвижной части формы 8. Как правило, отливка остается в подвижной половине преес-
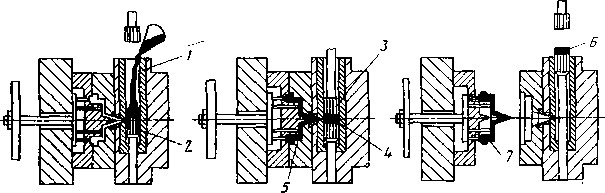
Рис. 1.2. Схема литья под давлением иа машинах с колодной вертикальной камерой прессовании
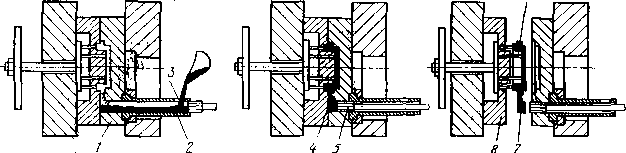
Рис. 1.3. Схема литья под давлением на машина» с колодной горизонтальной камерой прессования
формы, а затем выталкивается с помощью системы толкателей, либо сбрасывается в специальную тару, либо извлекается захватами манипулятора.
При литье по этой технологической схеме потери теплоты жидким металлом и гидравлическое сопротивление на пути его движения в полость пресс-формы меньше, чем при литье на машинах с вертикальной камерой прессования, в результате исключения одного из элементов литниковой системы — литникового хода. Это позволяет снизить температуру заливки сплава, уменьшить пористость отливки и осуществить ее эффективную подпрес-совку после окончания заполнения. Возможность широкого диапазона изменения скорости прессования позволяет создавать наиболее благоприятные гидродинамические и тепловые условия формирования отливки, до минимума сокращать пористость отливок.
В последние годы технология получения отливок на машинах с холодной горизонтальной камерой прессования получила наибольшее распространение как у нас в стране, так и за рубежом.
Впервые литье под давлением было применено Г. Бруссом в 1838 г. при изготовлении литер с изображением букв для газетопечатных машин. В 1839 г. был взят первый патент на поршневую машину для заливки металла под давлением. В машиностроении литье под давлением начали применять с 1849 г. для производства мелких деталей из оловянно-свинцовых сплавов. Машина конструкции В. Стуржиса, используемая для этих целей, имела ручной поршневой привод, с помощью которого в камере прессования, расположенной внутри тигля с расплавленным металлом, создавалось давление 100—150 Па. В 60-х годах прошлого века литье под давлением стали применять для изготовления отливок из сплавов на цинковой основе. В поисках повышения производительности ручной привод в поршневых машинах заменили пневматическим. В конце XIX в. были сделаны попытки использовать для литья под давлением алюминиевые, а затем и медные сплавы. По словам Л. Фроммера, «история развития литья под давлением есть в то же время история постепенного преодоления трудностей, возникавших благодаря применению все более тугоплавких и обладающих все более неблагоприятными литейными свойствами сплавов» [73].
т
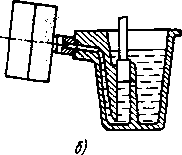
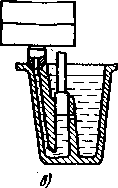
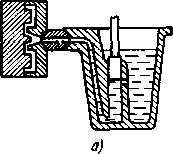
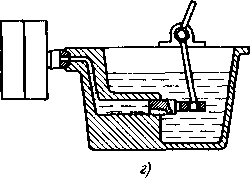
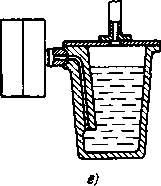
Рис. 1.4. Схемы поршневых и компрессорных машин
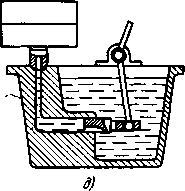
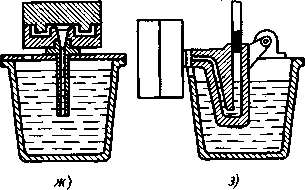
Все современные машины для литья под давлением по принципу работы узла прессования подразделяют на два класса: машины с горячей камерой прессования и машины с холодной камерой прессования. В свою очередь, машины с горячей камерой делятся по способу запрессовки металла в форму на поршневые и компрессорные.
Поршневые машины могут иметь вертикальную или горизонтальную камеру прессования. Поршневые машины с вертикальной камерой прессования подразделяют на машины с вертикальной (рис. 1.4, а), наклонной (рис. 1.4, б) и горизонтальной (рис. 1.4, в) плоскостью разъема пресс-формы. Машины с неподвижным горизонтальным металлопроводом могут иметь вертикальный (рис. 1.4, г) или горизонтальный (рис. 1.4, д) разъем формы. В современной практике поршневые машины с горячей камерой прессования и горизонтальной плоскостью разъема пресс-формы применяют крайне редко.
Машины, в которых движение металла осуществляется под действием сжатого воздуха, называют компрессорными. Первые конструкции этих машин, разработанные в конце прошлого века, были предназначены для изготовления отливок из алюминиевых сплавов. Принцип их работы заключается в том, что сжатый воздух давит на всю поверхность металла в тигле, из которого он поступает по неподвижному металлопроводу в пресс-форму с вертикальной (рис. 1.4, е) или горизонтальной (рис. 1.4, ж) плоскостью разъема. В настоящее время компрессорные машины такого тйпа выделились в отдельную группу машин для литья под низким давлением.
Компрессорные машины для литья под давлением с неподвижным металлопроводом были заменены машинами с подвижным металлопроводом, называемым гузнеком (рис. 1.4, з). В отличие от машин с неподвижным металлопроводом, в которых давление сжатого воздуха на металл не превышало 60 Па, в машинах с подвижным металлопроводом воздух давит на небольшую поверхность металла, находящегося в гузнеке, что дает возможность повысить давление до 400 Па. Кроме того, в гузнеке резко уменьшается поверхность окисления жидкого металла.
Машины с гузнеком не могли обеспечивать высокое качество отливок из сплавов на основе алюминия и быстро выходили из строя из-за разъедания стальных подвижных деталей камеры прессования. Их применяли главным образом для получения отливок из цинковых сплавов.
Принцип работы первых машин литья под давлением сохранился в одном из классов современных машин, получивших название машин с горячей камерой прессования. Но только создание машин с холодной камерой прессования позволило получить отливки из алюминиевых сплавов требуемого качества.
В первые десятилетия нашего века конструкции и качество изготовления пресс-форм уже отвечали требованиям по чистоте поверхности и точности размеров, предъявляемым к деталям машин и приборов. Технология изготовления деталей из проката механической обработкой оказалась значительно более трудоемкой, чем получение той же детали из литой заготовки. Кроме того, расход металла при этом снижался в 3—4 раза, поэтому совершенствование литья под давлением, которое позволяло получать заготовки по малоотходной и малооперационной технологии, шло по пути приближения отливки по конфигурации, размерам и шероховатости поверхности к готовой детали.
Производство продукции крупными сериями особенно способствовало развитию литья под давлением. Быстрая окупаемость затрат на оборудование и литейную оснастку ускорила процесс совершенствования и производства машин литья под давлением и пресс-форм.
В 1924 г. фирмы Ekkert (Германия) и Polak (Чехословакия) сконструировали и изготовили машины с холодной вертикальной камерой прессования. Это привело к широкому внедрению в массовое производство технологии изготовления отливок из алюминиевых, а затем и медных сплавов.
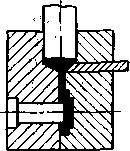
а)
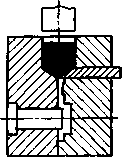
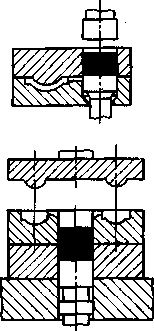
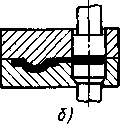
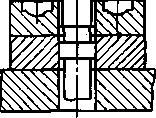
ШиМ
'Mi ■■ ■■ ЖЖА ЖЖЛ
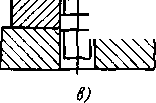
IW&k
s
I,
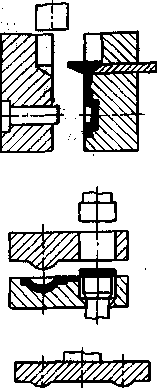
Рис. 1.5. Вертикальные камеры прессования
Существует несколько разновидностей вертикальных камер прессования. В 1939 г. в СССР была выпущена серия машин ОВП с холодной камерой, расположенной непосредственно в пресс-форме (рис. 1.5, а).
Фирмой Polak была изготовлена машина вертикальной компоновки мод. Р 100/100, в которой камера прессования размещалась в пресс-форме с горизонтальным разъемом (рис. 1.5, б), аналогичная машина мод. МЛ 50/50 была выпущена в СССР. С 1961 г. фирма Press Automatic (США) начала выпуск машин с вертикальным расположением запирающего механизма и вертикальной запрессовкой металла снизу по схеме, приведенной на рис. 1.5, в. Машины вертикальной компоновки с поворотом узла прессования и сегодня находят применение для получения отливок с повышенными требованиями по прочности и плотности (рис. 1.6). На машинах этого типа легко осуществлять автоматическую заливку и дозирование жидкого металла. Применяемая для машин данной конструкции схема спокойного заполнения снизу через утолщенные питатели не требует высокого давления, что позволяет получать крупногабаритные детали при сравнительно небольших усилиях запирания пресс-формы, эффективно
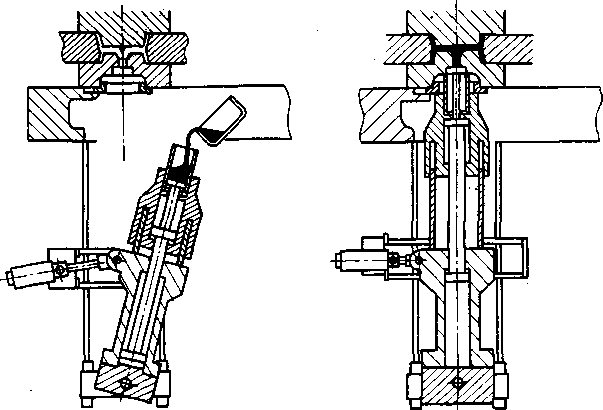
Рис. 1.6. Схема машины литья под давлением с вертикальной камерой прессования фирмы иЬе (Япония)
использовать подпрессовку. Машины вертикальной компоновки успешно применяют для изготовления роторов электродвигателей.
В СССР промышленное освоение литья под давлением началось в 20-е годы этого столетия. В 1923 г. А. Ф. Дурниенко изготовил пневматическую машину для литья под давлением цинковых сплавов и организовал в Москве мастерские по выпуску деталей замков и других бытовых изделий. В 1925 г. в Ленинграде на двух заводах инженер Б. Ю. Юнгмейстер организовал производство отливок под давлением на ручных машинах с горячей камерой. Здесь впервые начали изготовлять литые заготовки деталей приборов.
В 1929 г. работники завода «Изолит» С. Я. Ямщиков, А. П. Полянский, Н. А. Шубин, П. П. Кирьянов и другие создали на базе машин с горячей камерой прессования цех литья под давлением и разработали технические условия на поставку литья под давлением. /
В 1931 г. на одном из ленинградских заводов В. М. Пляцкий организовал участок литья под давлением, где на машинах с холодной камерой прессования было освоено производство деталей приборов сложной конфигурации из алюминиевых, цинковых и медных сплавов.
В 30-е годы было освоено производство отливок под давлением на Горьковском и Московском автомобильных заводах, на заводе «Автоприбор» в р. Владимире и др.
В 1940 г. завод «Красная Пресня» изготовил машину мод. ЛД-7 с вертикальной камерой прессования — это было началом отечественного производства необходимого для литья под давлением оборудования. Позже этим же заводом было освоено производство машин с горизонтальной холодной камерой прессования. Машины такого типа нашли наибольшее распространение в промышленности. Это объясняется простотой и надежностью конструкции такой камеры. Кроме того, в машинах с горизонтальной холодной камерой прессования потери теплоты жидким металлом и гидравлическое сопротивление на пути его движения в полость пресс-формы меньше, чем в машинах с вертикальной камерой, в результате исключения литникового хода. Это позволяет снизить температуру заливки сплава, уменьшить пористость и осуществить эффективную подпрессовку отливки после окончания заполнения формы. Машины с горизонтальной камерой прессования имеют более высокую производительность, чем машины с вертикальной камерой, так как поршень выталкивает пресс-остаток в момент раскрытия пресс-формы без дополнительных затрат времени.
Отечественное машиностроение выпускает машины с холодной горизонтальной камерой прессования с усилием запирания 1 ООО— 35 ООО кН. Большая часть современных машин имеет механизм прессования с мультипликацией давления рабочей жидкости в период подпрессовки. Различные конструкции и эксплуатационные характеристики механизмов прессования с мультипликаторами рассмотрены в работах [58, 32].
Дальнейшее совершенствование машин для литья под давлением направлено по пути повышения скоростей движения прессующего поршня с бесступенчатым регулированием скорости на различных этапах заполнения пресс-формы при одновременном снижении гидравлического удара в момент перехода от заполнения к подпрессовке. Отечественная промышленность выпускает в основном машины литья под давлением с холодной горизонтальной камерой прессования и автоматизированные комплексы и линии на их базе. Молдавское ПО «Точлитмаш» специализируется на выпуске машин с усилием запирания до 6000 кН, а ПО «Сиблитмаш» — до 35 ООО кН.
За рубежом машины литья под давлением и автоматизированные комплексы на их базе выпускают фирмы Vihorlat Snina (ЧССР), Litostroj (Югославия), фирма Bühler (Швейцария), JDRA, Itallpress, Triulzi (Италия), Frech, Weingarten (ФРГ), Toshiba, Ube (Япония), Lester, Sterling, Gabler (США) и др.
Важнейшей предпосылкой дальнейшего повышения количества отливок и эффективности литья под давлением является создание автоматизированных комплексов, гибких производственных систем и роторных линий литья под давлением, гибких автоматизированных производств [65].
Программами технического перевооружения предусматривается интенсивное обновление парка оборудования, применение
ЭВМ для управления процессами и производством, ужесточение требований техники безопасности, улучшение условий труда, повышение внимайия к охране окружающей среды.
1.2. ОСНОВНЫЕ ХАРАКТЕРИСТИКИ ПРОЦЕССА
При литье под давлением основными факторами, определяющими формирование отливки, являются давление в камере прессования и пресс-форме, скорости движения поршня и впуска жидкого металла в форму, параметры литниково-вентиляционной системы, температуры заливаемого металла и формы, режимы смазывания и охлаждения рабочей полости формы и камеры прессования.
Совокупность таких параметров, как давление в потоке металла, скорость движения металла, противодавление, возникающее вследствие затрудненного удаления воздуха и газообразных продуктов сгорания смазочного материала, образует гидродинамический режим формирования отливки. Температуры заливаемого сплава и формы, продолжительность заполнения и подпрес-совкй, а также темп работы определяют тепловой режим процесса.
От правильного выбора технологических режимов заполнения и подпрессовки, определяющих конструкцию пресс-формы, тип и мощность машины для литья под давлением, зависит качество отливок.
Теоретические основы процесса литья под давлением разработаны на основе проведенных научных исследований и накопленного производственного опыта. Они достаточно подробно изложены в работах [6, 73, 87, 85].
Гидродинамический режим формирования отливки создает кинетику заполнения, газовый режим формы, характер распределения газовых включений в отливке и качество рельефа ее поверхности. Давление в потоке металла возникает в результате сопротивления движению металла при прохождении его через тонкие сечения полости пресс-формы и обтекании стержней, при поворотах, сужениях и расширениях потока. В случае отсутствия сопротивления величина гидродинамического давления в потоке определяется противодавлением воздуха и газов, удаление которых затруднено из-за невозможности выполнения вентиляционных каналов большого сечения.
Четкость оформления рельефа и шероховатость поверхности отливки зависят от кинетической энергии потока. В момент окончания его движения создается гидродинамическое давление на стенки пресс-формы
Рф — Рм^ф’
где рм — плотность жидкого металла; — скорость потока в пресс-форме.
Высокая скорость впускаемого потока (скорость впуска) соответствует получению тонкостенных крупногабаритных отли-
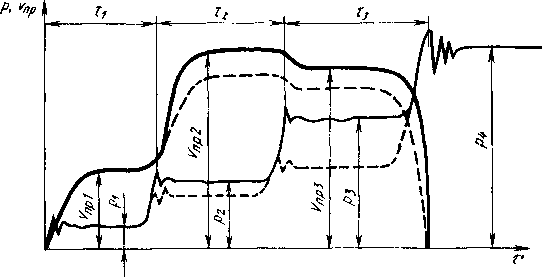
Рис. 1.7. Изменение скорости прессующего поршня и давления в цилиндре прессования за время кода поршня
вок сложных очертаний. Высокие скорости впуска и потока в пресс-форме создаются в результате быстрого перемещения прессующего поршня. Для преодоления сопротивления затвердевающей массы металла в тонких сечениях оформляющей полости, а также сопротивления газов, остающихся в отливке, необходимо высокое гидростатическое давление. Оно передается от прессующего поршня через литниковый питающий канал. Чем позже затвердеет питатель, тем продолжительнее действие давления. Процесс передачи гидростатического давления в полость пресс-формы называется подпрессовкой. Использование утолщенных питателей позволяет осуществить подпрессовку и питание отливки жидким металлом в период кристаллизации и тем самым устранить усадочные раковины.
Процесс движения металла в камере прессования и пресс-форме можно разбить на четыре фазы. На рис. 1.7 приведены кривые изменения скорости опр перемещения прессующего поршня и давления р рабочей жидкости в цилиндре прессования за время хода поршня. Если пресс-форма заполняется сплошным потоком, то изменение давления металла в ее полости будет подобно изменению давления жидкости в цилиндре. За время поршень перекрывает заливочное отверстие (фаза /). Скорость поршня опр1 небольшая. Значение р1 соответствует давлению, необходимому для преодоления трения в гидравлическом цилиндре и камере прессования. Период т2 (фаза II) соответствует заполнению металлом под действием поршня всего объема камеры прессования, вплоть до литниковых каналов. Скорость поршня начинает возрастать и достигает максимального значения опр2 (на машинах
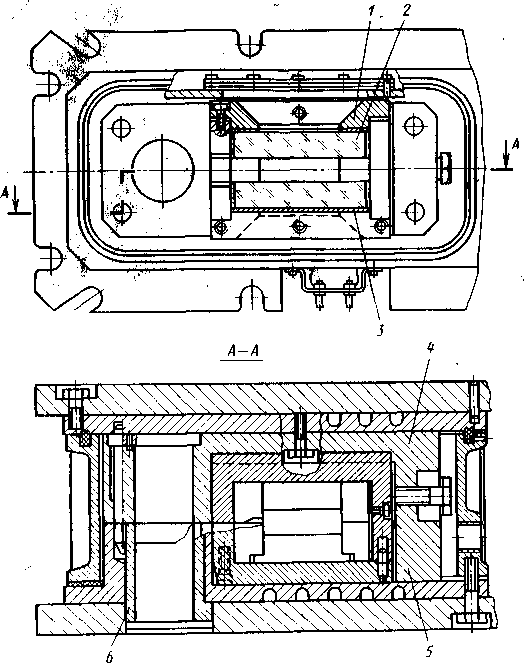
Рис. 1.8. Пресс-форма для киносъемки процесса заполнения:
1 — пластина с отверстием для крепления стекла; 2 — закаленное жаропрочное стекло; 3 — свинцовая прокладка; 4 и б — неподвижная и подвижная половины пресс-формы; 6 —. литниковая втулка
современных моделей возможна еще одна ступень повышения скорости в период заполнения). Давление р2 больше рг на величину гидравлических сопротивлений в камере прессования.
В период времени т3 (фаза III) заполняется литниковая система и полость пресс-формы. Вследствие резкого сужения потока в питателе скорость падает до опрз, а давление р3 повышается. При меньших значениях максимальной скорости давлейие в фазах II и III также падает (штриховые линии). В момент окончания хода поршня происходит гидравлический удар вследствие итерационных сил подвижных частей прессующего механизма, давление возрастает. После затухания колебания устанавливается конечное гидростатическое давление р4 и начинается фаза IV — подпрес-совка. Величина конечного давления зависит от рода сплава, его состояния (вязкости, плотности), требований к отливке и других факторов. Она может изменяться от 0,50 до 50 кПа. Если к моменту достижения давления р4 металл в питателе остается жидким или, как принято называть, жидкоподвижным, то это давление передается на затвердевающую отливку.
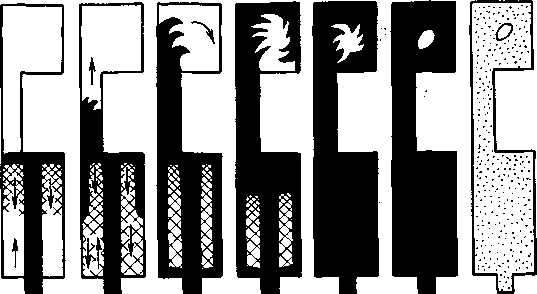
Рис. 1.9, Схема дисперсно-турбулентного заполнения
ш......
г 5 9 Я 59 67 75 900-10, С
Максимальное усилие подпрессовки должно развиваться прессующим механизмом машины не в момент начала затвердевания отливки, а практически сразу по окончании заполнения пресс-формы.
Характер движения металла в оформляющей полости зависит от скорости впуска, соотношения толщин питателя и отливки, вязкости и поверхностного натяжения заливаемого сплава, тепловых условий его взаимодействия со стенками пресс-формы. На основе скоростных киносъемок процесса движения металла в прозрачной пресс-форме (рис. 1.8), результаты которых подробно рассмотрены в работах [6, 73], установлено, что при литье с малыми скоростями впуска возможно заполнение даже ламинарным потоком, со средними скоростями — сплошное турбулентное заполнение. При высоких скоростях впуска поток разбивается, заполнение становится дисперсным. Однако заполнение полости формы ламинарным, турбулентным или дисперсным потоком возможно лишь при получении образцов или отливки простой формы.
Большая часть отливок, используемых в машиностроении и приборостроении, имеет сложную конфигурацию с локальными утолщениями, бобышками, приливами и переходами, поэтому даже дисперсное заполнение в чистом виде наблюдается очень редко. Реальное заполнение отливок сложной конфигурации представляет собой последовательное превращение дисперсного потока, образовавшегося в месте удара струи о стенку формы, в сплошной турбулентный подпор, как это показано на рис. 1.9.
Таким образом, часть полости формы заполняется дисперсным потоком, а удаленные от питателя сечения полости заполняются сплошным турбулентным потоком. Соотношение дисперсных и турбулентных потоков зависит от скорости впуска, толщины отливки и сложности конфигурации, главным образом от числа поворотов в полости формы [71.
Тепловой режим процесса формирования отливки при литье под давлением обеспечивает подвижность сплава как в период заполнения формы, так и в процессе подпрессовки. Он связан с высокой интенсивностью теплового взаимодействия ЖИДКОГО металла со стенками массивной пресс-формы.
Процесс охлаждения металла можно разделить на два периода. Первый — охлаждение жидкого металла при движении его в литниковой системе и оформляющей полости. На этом этапе важно правильно выбрать продолжительность заполнения, чтобы предупредить образование неслитин, пористости и оксидных плен. Второй период — затвердевание металла после заполнения пресс-формы. На этом этапе необходимо создать условия направленного затвердевания металла отливки. Соблюдение принципов направленного затвердевания во многом зависит от технологичности конструкции отливки, температуры заливаемого сплава и температуры пресс-формы.
Тепловой режим определяет не только качество отливок, но и стойкость формы. Одна из основных причин разрушения поверхностных слоев матриц и пуансонов и появление на отливках так называемых следов разгара формы — это возникновение температурных напряжений во вкладыше. Долговечность пресс-формы, как показали результаты исследований В. Т. Рождественского, зависит от величины максимальных температурных напряжений и коэффициента линейного температурного расширения материала пресс-формы. Кроме того, она снижается из-за активного силового взаимодействия между охлаждающимся сплавом и нагревающимися рабочими частями формы.
Тепловой режим, определяющий условия формирования отливки, связан с высокой скоростью затвердевания жидкого металла, которая возрастает при охлаждении формы водой или терморегулирующей жидкостью. Терморегулирование рабочей полости пресс-формы необходимо для стабилизации и выравнивания тепловых условий в различных по толщине сечениях ОТЛИВКИ.
Для обеспечения свариваемости отдельных потоков металла до его затвердевания с целью предупреждения несливди, пористости и оксидных плен продолжительность заполнения не должна превышать доли секунды. При разработке теплового режима большое значение имеет расчет продолжительности заполнения формы. Как отмечалось выше, отливки сложной конфигурации заполняются последовательно дисперсно турбулентным потоком. В этом случае продолжительнрсть заполнения тзап определяется при условии, что дисперсный характер движения соответствует первому периоду заполнения, а турбулентный второму. По продолжительности заполнения, определенной на основании рассмотрения тепловых условий в форме, подсчитывают технологическую скорость прессования
®пр = тотл1(РыР пр^зап)»
где тотл —■ масса отливки; Fap —< площадь поперечного сечения камеры прессования.
При создании благоприятных тепловых условий, обеспечивающих сохранение жидкотекучести металла в литниковых каналах и полости формы, особенно в наиболее тонких ее сечениях, возможно осуществить подпрессовку. Наиболее эффективно подпрес-совка используется на машинах с горизонтальной камерой прессования. Подпрессовка в процессе кристаллизации сплава сжимает газовые включения, уменьшает усадочную пористость и улучшает структуру металла [81.
Эффективность подпрессовки зависит от продолжительности достижения максимального значения давления в процессе кристаллизации сплава. Чем меньше это время, тем выше эффект подпрессовки. Современные гидравлические схемы машин литья под давлением позволяют добиться снижения времени подпрессовки до 0,016 с. На основании расчета гидродинамического и теплового режимов процесса определяют параметры прессующего механизма машины литья под давлением. Машины для литья под давлением должны иметь механизм или систему подачи рабочей жидкости в прессующий цилиндр, обеспечивающую заданное конечное давление при подпрессовке. Чаще всего для этого используют мультиплицирующие механизмы, которые позволяют не только повысить давление, но и уменьшить пиковое давление гидравлического удара.
Раскрытие и закрытие пресс-формы осуществляются запирающим механизмом, который одновременно используется и для выталкивания отливки. В современных конструкциях машин литья под давлением применяют запирающие механизмы четырех типов: гидравлические, гидрорычажные, гидроклиновые и комбинированные (гидроклинорычажные).
Наиболее широко распространены гидрорычажные запирающие механизмы [581.
1.3. НОМЕНКЛАТУРА ОТЛИВОК, ПОЛУЧЕННЫХ ЛИТЬЕМ ПОД ДАВЛЕНИЕМ
Литье под давлением занимает одно из ведущих мест в литейном производстве. В отечественной и зарубежной практике этим способом получают отливки, по конфигурации и размерам наиболее близкие к готовым деталям из цинковых, алюминиевых, магниевых и медных сплавов.- Изготепление отливок из стали, чугуна, титановых и других тугоплавких сплавов еще не получило широкого применения, что объясняется в основном низкой I •' 1
18 * ' стойкостью оформляющих частей и высокой стоимостью материалов для пресс-форм.
Производство отливок из алюминиевых сплавов в различных странах составляет 30—50% общего выпуска (по массе) продукции литья под давлением. Следующую по количеству и разнообразию номенклатуры группу отливок представляют отливки из цинковых сплавов. Магниевые сплавы для литья под давлением применяют реже, что объясняется их склонностью к образованию горячих трещин и более сложными технологическими условиями изготовления отливок. Однако следует отметить, что отливки из магниевых сплавов почти в 1,5 раза легче отливок из алюминиевых сплавов и лучше обрабатываются резанием, причем магний не налипает на поверхности стальных пресс-форм и не приваривается к ним. Получение отливок из медных сплавов ограничено низкой стойкостью пресс-форм.
Номенклатура выпускаемых отечественной промышленностью отливок очень разнообразна. Этим способом изготовляют литые заготовки самой различной конфигурации массой от нескольких грамм до нескольких десятков килограмм.
Современные конструкции машин литья под давлением, создающие давления на металл до 800 МПа и скорости прессования до 7 м/с, позволяют получать крупногабаритные и сложные по конфигурации отливки, например блок цилиндров автомобиля «Москвич» массой 18,6 кг. Эти отливки изготовляют из сплава системы алюминий—кремний—медь на машине с усилием запирания 20 000 кН. В отливках множество литых отверстий, толщина стенки 4—5 мм. Они проходят испытания на герметичность при давлении 15 МПа. Пресс-форма для такой отливки весит около 2 т. Применение эффективной подпрессовки дает возможность получать очень плотные герметичные детали, такие, как алюминиевый корпус отопительной батареи. Заполнение этой тонкостенной крупногабаритной отливки металлом сопровождается активным захватом газов из полости пресс-формы, однако высокое давление (выше 400 МПа) обеспечивает высокую степень сжатия воздушных и газовых включений. Применение такой отливки не только снижает массу отопительной системы, улучшает теплообмен, экономит энергоресурсы и металл, повышает производительность труда и снижает себестоимость продукции, но и облагораживает интерьер.
Некоторые отливки имеют сложные криволинейные поверхности и каналы, которые при заданных точности и шероховатости и экономической целесообразности не могут быть выполнены никакими другими способами, кроме как литьем под давлением, например головка блока цилиндров (рис. 1.10, а) и диск вентилятора компрессора (рис. 1.10, б). Эти отливки имеют значительную толщину стенки (до 12 мм), что позволяет использовать направленное затвердевание, при увеличенной толщине питателя, создающего оптимальные гидродинамические и тепловые условия подпрессовки [1341. |
Разработанные в отечественной промышленности технология и оборудование литья под давлением позволяют получать отливки, толщина стенки которых в некоторых местах равна 1 мм, например детали фотоаппаратуры. На специально созданной специализированной машине и с применением вакуума, термостатиро-вания формы и других технологических приемов были получены отливки с толщиной стенки 0,6 мм [21].
Расширяется область применения литья под давлением магниевых сплавов. Наряду с использованием этих сплавов для корпусных деталей пишущих машинок, приборов, биноклей, фото- и киноаппаратуры, бензопил они успешно применяются в автомобилестроении и авиационной технике для деталей, несущих определенную нагрузку. Например, фирма Volkswagen (ФРГ) изготовляет из магниевых сплавов диски колес спортивных автомобилей, а Мелитопольский завод «Автоцветлит» — детали мотора автомобиля «Запорожец». Литьем под давлением можно получать отливки с внешней или внутренней резьбой: барашковые гайки и винты, колпачковые гайки, винты и гайки с фигурными головками, штепсельные разъемы и др. Литая резьба значительно прочнее, чем полученная механической обработкой, так как при нарезании резьбы удаляется наиболее плотный поверхностный слой отливки. Литая резьба также имеет более постоянный профиль, который является негативным отпечатком резьбовой вставки пресс-формы, выполняемой с точностью, значительно превосходящей обычную точность обработки на резьбонарезных станках. Качество поверхности литой резьбы выше, чем механически нарезанной, так как рабочие поверхности пресс-формы шлифуют и полируют. Литьем под давлением можно изготовлять отливки со специальной резьбой, которую почти невозможно получить другим способом, например прямоугольную или спиральную резьбу треугольного профиля для ниппелей, ввинчиваемых в гибкие шланги.
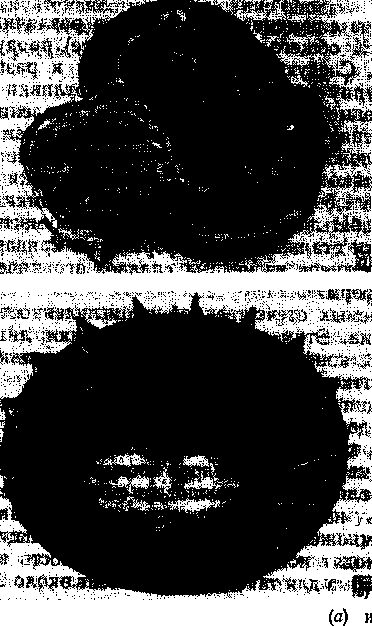
Рис. 1.10. Головка блока цилиндров диск вентилятора (б) компрессора
Литьем под давлением можно получать отливки с разнообразной арматурой из стали, чугуна, меди, бронзы и других материалов. Армирование отливок пустотелыми вкладышами или криволинейными трубками позволяет получать каналы и полости сложнейшей конфигурации.
Наряду с конструкторскими задачами, армирование помогает решать ряд технологических проблем. Например, использование арматуры в качестве холодильников позволяет регулировать процесс затвердевания массивных частей отливки. Армирование отливок стальными и чугунными элементами дает экономию дефицитных цветных сплавов. Армированное литье под давлением позволяет во многих случаях заменить сборку отдельных узлов изделий.
Отливки из алюминиевых, магниевых и медных сплавов, так же как и отливки из чугуна, стали и титановых сплавов, получают главным образом на машинах с холодной камерой прессования. Отливки из цинковых сплавов изготовляют преимущественно на машинах с горячей камерой прессования.
Отливки из цинковых сплавов наиболее часто используют в производстве автомобилей и товаров народного потребления (дверные и мебельные замки, зажимы застежек «молния», детали швейных машин и др.). В автомобильной промышленности из цинковых сплавов изготовляют детали приборов и декоративные детали типа ручек, решеток, корпусов фар и пр. Благодаря хорошим литейным свойствам и высокой механической прочности этих сплавов из них можно делать крупные и тонкостенные детали. Например, панель облицовки радиатора автомобиля Dodge (США) имеет массу 9 кг и длину 1790 мм при толщине стенки 1,8 мм. В отечественной промышленности самой крупной деталью из цинкового сплава, изготовляемой на машине с горячей камерой прессования, является решетка радиатора автомобиля «Жигули». Отливка имеет массу 2,7 кг, длину 1054, ширину 270 мм и среднюю толщину стенки 1,25 мм.
В настоящее время процесс литья под давлением развивается в трех направлениях, обусловленных конфигурацией отливок и требованиями к их качеству:
литье с низкими скоростями впуска через толстые питатели, обеспечивающие заполнение пресс-формы сплошными потоками и эффективную подпрессовку; применяют для получения толстостенных отливок несложной конфигурации, к которым предъявляют высокие требования по прочности и герметичности;
литье с высокими скоростями впуска через тонкие питатели с образованием дисперсного заполнения; применяют для получения тонкостенных отливок сложной конфигурации, к которым предъявляют высокие требования по качеству поверхности и четкости рельефа;
литье со средними скоростями впуска с образованием совмещенных турбулентных и дисперсных потоков; требует обязательной подпрессовки; применяют для получения отливок с неравномерной толщиной стенок; пористость уменьшают установкой фильтров, промывников или изменением газового режима пресс-формы.
В большинстве случаев для получения отливок используются универсальные машины литья под давлением, однако, исходя из требований к отливкам и из условий производства, могут применяться специализированные машины литья под давлением. Например, машины с вакуумными устройствами, с устройствами для продувки кислорода со сдвоенным поршнем, для литья стали или для получения какой-то одной, очень сложной или специфичной отливки, например машины для ступеньки эскалатора, машины для заливки ротора электродвигателей.
2 КОНСТРУИРОВАНИЕ ОТЛИВОК
2.1. СПЛАВЫ
Для литья под давлением наиболее широко используют алюминиевые сплавы, имеющие хорошее сочетание физических, механических и технологических свойств. Второе место по объему выпуска отливок занимают цинковые сплавы, затем магниевые и медные. Литье сплава каждого типа осуществляется по определенной технологии процесса и, как правило, на оборудовании, соответствующем особенности сплава. В табл. 2.1 дана сравнительная оценка сплавов по 5-балльной шкале, основанная на их физических, механических и литейных свойствах. Лучшие свойства соответствуют 5 баллам.
Физические и механические свойства сплавов, а также параметры процесса приведены в табл. 2.2.
Целям повышения рентабельности производства, обеспечения централизации плавильного отделения и стабилизации технологических режимов служит унификация сплавов. Многие крупнейшие производства стремятся использовать всего один или два сплава. Анализ литературных и производственных данных показывает, что в качестве основных можно принять алюминиевые сплавы АЛ2, АЛ4 и АЛ32, цинковые ЦА4 и ЦА4М1, магниевый МЛ5, латуни ЛЦ40Сд и ЛЦ40МцЗЖ-
Алюминиевые сплавы. На первой стадии развития литья под давлением в СССР применяли используемый для литья в кокиль сплав АЛ9 (7% и 0,3% Mg). Однако в отливках, полученных литьем под давлением, имела место повышенная пористость, поэтому стали использовать сплавы АЛ2 (12% Б1) и АЛ4 (9% Б1 и 0,3% Mg) (ГОСТ 2685—75). Сплав АЛ2 обладает высокой жид-котекучестью, хорошими коррозионной стойкостью, теплопроводностью и электрической проводимостью. Его используют главным образом для крупных, сложных и тонкостенных отливок. К недостаткам сплава относятся плохая обрабатываемость резанием и более низкие по сравнению со сплавами, легированными магнием, медью и другими компонентами, механические свойства.
Сплав АЛ4 незначительно уступает сплаву АЛ2 по литейным свойствам, но обладает более высокими механическими свойствами, хорошей обрабатываемостью резанием и высокой коррозионной стойкостью. Он широко применяется и при изготовлении отливок литьем в кокиль. '
Сплавы | ||||
Показатель | ||||
алюми |
цин |
магни |
медные | |
ниевые |
ковые |
евые |
Физические свойства
Температура плавлення |
3 |
5 |
3 |
2 |
Плотность |
4 |
3 |
5 |
2 |
Теплопроводность |
4 |
3 |
2 |
4 |
Сопротивляемость коррозии |
4 |
3 |
2 |
4 |
Механические свойства | ||||
Временное сопротивление разрыву |
2 |
3 |
2 |
4 |
Предел текучести |
3 |
2 |
3 |
4 |
Относительное удлинение |
2 |
3 |
2 |
5 |
Ударная вязкость |
2 |
3 |
2 |
5 |
Литейные свойства | ||||
Жидкотекучесть |
4 |
5 |
4 |
3 |
Склонность к образованию трещин |
4 |
5 |
3 |
4 |
Склонность к привариванию |
3 |
5 |
5 |
4 |
Минимально допустимая толщина стен |
4 |
5 |
4 |
3 |
ки отливки |
2.2. Свойства сплавов и параметры процесса литья под давлением
Показатель |
Сплавы | |||
алюминиевые |
цинковые |
магниевые |
медиые |
Содержание элемента, % (остальное А1)
Сплав |
Си |
мг |
Мп |
Ті | |
АЛ32 (ГОСТ 2685—75) А380.0 (США) А360.0 (США) |
7.5—8,5 7.5—9,5 9,0—10,0 |
1.0—1,5 3.0—4,0 0,6 |
0,3—0,5 0,10 0,4—0,6 |
0,3—0,5 0,50 0,35 |
0,1—0,3 |
В 60-е годы в СССР специально для литья под давлением был разработан сплав АЛ32, который относится к сплавам системы А1—Б!—Си—с добавками Мп и Тс Химический состав этого сплава и содержание тех же элементов в сплавах, широко применяемых в США, приведены в табл. 2.3. Эти сплавы применяют для получения высокопрочных деталей литьем под давлением, в том числе блока цилиндров автомобильных двигателей. Меньшее содержание меди в сплавах АЛ32 и А360 обеспечивает более высокую коррозионную стойкость. Сплавы этой системы обладают хорошей жидкотекучестью и высокими механическими свойствами, легко обрабатываются резанием.
В тех случаях, когда решающим фактором является высокая коррозионная стойкость, применяется сплав АЛ27 (10% Mg), который отлично сопротивляется коррозии в растворах щелочей и в кислотах, а также обладает высокими механическими свойствами и хорошей обрабатываемостью резанием. Однако этот сплав обладает низкими технологическими свойствами и требует выдерживания технологических параметров литья в узких пределах. Возможность его применения ограничивается сложностью конфигурации отливки, он ие относится к группе тех сплавов, которые используют для унификации. Следует учитывать, что при высоких требованиях, когда не допускаются даже слабые следы коррозии, рекомендуется не переход на коррозионно-стойкий сплав, а специальная защита поверхности деталей.
Литейные, технологические и эксплуатационные свойства рассмотренных сплавов приведены в табл. 2.4. Интервал кристаллизации сплава АЛ32 593—538 °С, сплава АЛ2 582—574 °С, сплава АЛ4 596—577 °С, сплава АЛ27 621—535 °С. Следует учитывать, что узкоинтервальные сплавы обеспечивают получение отливок с мелкозернистой эвтектикой. Литейщики обычно отдают предпочтение этим сплавам благодаря их хорошим литейным свойствам. Однако современные машины с механизмами, обеспечивающими эффективную подпрессовку, позволяют изготовлять. качественные отливки из широкоинтервальных сплавов, причем более продолжительный период затвердевания дает воз-вожность полнее использовать давление подппессовки для уплотнения металла отливки. ^
Свойства |
АЛ32 |
АЛ2 |
АЛ4. АЛ4В |
АЛ27 |
Жидкотекучесть |
4 |
5 |
4 |
3 |
Усадка |
4 |
5 |
5 |
2 |
Склонность: | ||||
и образованию горячих трещин |
4 |
4 |
4 |
4 |
к образованию дефектов поверхности |
4 |
2 |
3 |
3 |
к привариванию к пресс-форме |
4 |
5 |
3 |
2 |
Герметичность отливок |
3 |
5 |
5 |
3 |
Обрабатываемость резанием |
4 |
2 |
3 |
5 |
Полируемость |
4 |
2 |
4 |
5 |
Коррозионная стойкость |
2 |
3 |
4 |
5 |
Механические свойства алюминиевых сплавов АЛ2, АЛ4, АЛ32 и ВАЛ8 измерялись в пяти крупных цехах литья под давлением. Временное сопротивление разрыву ав отлитых под давлением плоских образцов исследованных сплавов после их старения колебалось от 200 до 350 МПа. Наименее прочным и наиболее пластичным был признан сплав АЛ2. Временное сопротивление образцов из этого сплава не превышало 280 МПа, причем 43% всех образцов имели прочность только 200—240 МПа. Значение ав сплава АЛ4 несколько выше и достигает 300 МПа, а 24% образцов имеют значения в пределах 200—240 МПа, что значительно ниже, чем у сплава АЛ2.
Более прочны сплавы АЛ32 и ВАЛ8, 80% образцов из сплава АЛ32 имеют сгв = 260-т-ЗЗО МПа.
Необходимо отметить небольшое относительное удлинение 6, которое у сплавов АЛ4, АЛ32 и ВАЛ8 в 80—90% всех случаев не превышает 1 % и только у сплава АЛ2 удлинение более 1 % имеют 70% образцов.
В некоторых случаях применяют сплавы других марок, например, для деталей штепсельных разъемов — сплав АЛ11 (6—8% 51, 0,1—0,3% Mg, 7—12% 2п), для деталей мопедов сплав АК5М7 (4,5—6,5% 51, 0,2—0,5% Мд и 6—8%. Си).
Цинковые сплавы. Хорошие литейные свойства цинковых сплавов позволяют получать самые сложные отливки со стенками толщиной менее 1 мм. Кроме того, цинковые сплавы не взаимодействуют с металлом пресс-формы и деталей камеры прессования, что позволяет применять высокопроизводительные автоматические машины с горячей камерой прессования. Низкая температура плавления (380—390 °С) этих сплавов и возможность литья при невысоких давлениях прессования обеспечивают высокую стойкость пресс-форм — 50 000 и даже 1 млн. циклов. Все эго обеспечивает низкую себестоимость отливок из цинковых сплавов. Еще одним существенным преимуществом этих сплавов является возможность нанесения декоративных, антикоррозионных и упрочняющих покрытий практически всех видов, т. е. производить меднение, никелирование, кадмирование, хромирование без предварительной отделки Поверхности отливок.

ЦА4о Хорошие коррозионная стойкость и
стабильность размеров ЦА4 Хорошая стабильность размеров, но
меньшая, чем у сплава ЦА4о, коррозионная стойкость ЦА4М1о Хорошая коррозионная стойкость,
неизменяемость (практически) размеров при естественном старении
ЦА4М1 Хорошая коррозионная стойкость, но
меньшая, чем у сплава ЦА4М1о, стабильность размеров ЦА4МЗ Высокая прочность (сгв = 290 МПа),
изменяемость размеров до 0,5%, пониженная коррозионная стойкость
Для деталей приборов, требующих стабильности размеров
Для корпусных, арматурных и декоративных деталей, не требующих повышенной прочности
Для деталей с повышенной прочностью
Наиболее часто применяют I сплавы ЦА4 и ЦА4М1 (ГОСТ 25140—82). В отдельных случаях применяются сплавы ЦА4о и ЦА4М1о повышенной чистоты, а также сплав ЦА4МЗ повышенной прочности (ав = 290 МПа, 6 = 1,5%). Отливки из сплава ЦА4 отличаются высокой точностью и стабильностью размеров. Сплав ЦА4М1 обладает более высокими механическими свойствами, чем сплав ЦА4, но стабильность размеров изготовленных из него отливок ниже. Интервал кристаллизации сплавов ЦА4 и ЦА4М1 386—380 °С, а сплава ЦА4МЗ 389—379 °С. Плотность сплавов ЦА4 и ЦА4М1 равна 6700 кг/м3, а сплава ЦА4МЗ — 6800 кг/м3.
На ранней стадии развития литья под давлением, начиная с 60-х годов прошлого столетия, применению цинковых сплавов препятствовало их старение, приводящее к нестабильности размеров отливок, а также низкая сопротивляемость коррозии. Нередко отливки разбухали, деформировались, растрескивались, а в некоторых случаях и полностью разрушались. Причиной этого была очень высокая чувствительность цинковых сплавов к примесям (свинец, кадмий, олово), влияющим на образование межкристаллитной коррозии, распространяющейся по границам зерен. Примеси располагаются по границам зерен вследствие весьма малой растворимости. Свинец не растворим в цинке даже в жидком состоянии. Факторами, способствующими протеканию коррозии, являются влажность и особенно водяные пары. Продукты межкристаллитной коррозии, занимающие больший, чем металл, из которого они образовались, объем1, приводят к разбуханию, короблению и разрушению отливок.
Марка сплава |
<7В, МПа |
в, % |
НВ, МПа |
Не мевее | |||
ЦА4о, ЦА4 |
256 |
1,8 |
700 |
ЦА4М1о, ЦА4М1 |
270 |
1,7 |
800 |
ЦА4МЗ |
290 |
1,5 |
900 |
Проблема получения отливок, обладающих высокой стойкостью к атмосферному воздействию, решена применением технически чистого цинка (99,99% Ъп). Другие металлы, используемые для выплавки цинковых сплавов, должны иметь следующую чистоту: алюминий — 99,75%, магний — 99,8%, медь — 99,9%. Свойства и область применения сплавов приведены в табл. 2.5 и 2.6.
В последнее время исследуют и внедряют в производство сплавы с высоким содержанием алюминия, условно обозначенные за рубежом 2А-8, 1к-\2 и 1к-27 (табл. 2.7). В маркировке сплава цифра указывает на среднее содержание алюминия в процентах. Механические свойства сплавов, приведенные в таблице, даны по результатам опытной работы.
Из-за повышенного содержания алюминия для литья используют машины не с горячей, а с холодной камерой прессования. Сплав Ък-27 нельзя использовать для изготовления отливок, имеющих толстые сечения. Сплав Ък-8 наилучший из рассматриваемых по легкости выполнения финишной обработки и нанесения гальванопокрытий. Сплавы ЪкЛ2 и Ък-27 отличаются высокой износостойкостью, и для отливок, имеющих узлы трения, отпадает необходимость в применении стальных или бронзовых вставок.
Применение высокоалюминиевых цинковых сплавов позволяет экономить цинк и снижать массу отливок с соответствующим экономическим эффектом. При внедрении сплавов в производство требуется отработка технологического процесса литья, а также режимов резания и нанесения гальванопокрытий. В СССР разработаны технические условия на цинковый литейный сплав марки ЦА27М1. Сплав обладает следующими свойствами: ав = = 400-г440 МПа; 6 = 0,5-ь1,5%, НВ = 2200-Г-1200 МПа, плотность 5000 кг/м3. Температурный интервал затвердевания этого сплава 483—375 °С, у сплавов Ък-\2 и Ък-8 он соответственно равен 432—375 и 403—375 °С.
Магниевые сплавы. Одним из преимуществ магниевых сплавов является то, что при малой плотности они обладают механическими свойствами на уровне алюминиевых сплавов. Для литья под давлением наиболее пригодны сплавы системы ^—А1—Ъп. В СССР чаще всего применяют сплав МЛ5 (ГОСТ 2856—79), который
Свойства сплавов
580—600 |
380—400 |
580—585 |
900—950 |
2500—2700 |
6600—7000 |
1750—1850 |
7900—8800 |
160—280 |
250—300 |
160—230 |
300—400 |
1—3 |
1—3 |
1—2 |
15—40 |
600—900 |
700—800 |
500—600 |
800—1000 |
Температура плавления, °С
Плотность, кг/м3 Временное сопротивление разрыву, МПа Относительное удлинение, %
Твердость НВ, МПа
Параметры процесса
Температура заливки, °С |
580—630 |
380—420 |
600—660 |
900—950 |
Отклонение размеров от |
±0,15 |
±0,10 |
±0,15 |
±0,25 |
ливки, % | ||||
Стойкость пресс-формы, |
50 000 |
500 000 |
. 70 000 |
5000 |
число циклов |
обладает следующими механическими свойствами сгв = 171,5 МПа 6 = 2% и НВ = 500 МПа. За рубежом применяют сплавы по составу и механическим свойствам очень близкие к сплаву МЛ5.
Интервал температур кристаллизации сплава МЛ5 607—492 °С. Широкий интервал температур кристаллизации и одновременно быстрое охлаждение сплава обеспечивают получение отливок с мелкозернистой структурой, характеризующихся высоким относительным удлинением и хорошей ударной вязкостью. Сопротивление ударным и вибрационным нагрузкам не снижается даже при отрицательных температурах. Поэтому литьем под давлением из сплава МЛ5 изготовляют такие детали, как рукоятки бензопил и буров. Опыт литья деталей из сплава с повышенным содержанием цинка (до 2%) показал, что, несмотря на высокую жидкотекучесть, этот сплав неприемлем для литья под давлением из-за его чрезмерной хрупкости в горячем состоянии. Наилучшие сочетания механических свойств имеют сплавы, содержащие не более 0,3% 2п. В европейские стандарты включены магниевые сплавы, вообще не содержащие цинка, предназначенные для изготовления отливок, работающих при больших ударных нагрузках.
В отличие от алюминиевых, магниевые сплавы в жидком состоянии практически не привариваются к рабочим поверхностям пресс-формы, что резко снижает эрозию матриц и повышает их стойкость более чем на 50%. Магниевые сплавы обладают меньшей жидкотекучестью и хуже заполняют форму, чем сплавы на основе алюминия, цинка, меди. Это затрудняет получение отливок с очень тонкими стенками. Кроме того, магниевые сплавы имеют повышенную склонность к образованию горячих трещин в местах затрудненной усадки, что требует более тщательной отработки технологических режимов литья.
Магний больше, чем другие промышленные металлы, склонен к окисле-
я
X/
НВ, МПа |
1030±26 1000±50 1190±30 |
в. % |
ю •н-н- 00 ш |
• 03 |
іо © 00 -н-н-н о о —• © О* 04 СО СО |
й! |
00 ^.со" <М Ю — -н-н-н ^ ^ <о С"- О СО ^ |
§ чэ в> в |
0) V 0) — 40 «м О О^о .-о .- с .„с </) соо со 00 со о со о ©о© |
в 8 3 в о. с |
"О ♦ иди 8§8 °"©‘^ о« р, о* ©о ® о о о |
ьо г |
0,015-0,03 0,015—0,03 0,01—0,02 |
3 и |
0,8—1,3 0,5—1,25 2,0—2,5 |
< ' |
8,0—8,8 11.0—11,5 25.0—28,0 |
Сплав |
2А-8 2А-12 1А-27 |
нию. Сплавы магния достаточно устойчивы в чистой фтористо-водородной кислоте любой концентрации и едких щелочах, но они сильно корродируют во всех других растворах кислот и солей, а также в обычной и особенно в морской воде. Незащищенные поверхности отливок из магниевых сплавов очень быстро окисляются даже на воздухе, поэтому на поверхности деталей из магниевых сплавов наносят защитные покрытия. Основным способом нанесения покрытий является оксидирование в растворах, содержащих соли хрома. На детали, работающие при температуре 100—200 °С, наносят дополнительно лакокрасочные покрытия.
Медно-цинковые сплавы. Из медных сплавов для литья под давлением применяют главным образом латуни, которые по сравнению с бронзами обладают лучшей жидкотекучестью и значительно меньшей усадкой. Наиболее часто используют свинцовую латунь ЛЦ40Сд (ГОСТ 17711—80), содержащую 58—61% Си и 0,8—2,0% РЬ. Эта латунь хорошо обрабатывается резанием из-за наличия свинца, поэтому ее применяют для литья деталей газовой, санитарной, гидравлической и пневматической аппаратуры (втулки, тройники, переходники, сепараторы подшипников), работающих в среде воздуха и пресной воды.
Для изготовления несложных по конфигурации деталей ответственного назначения и арматуры морского судостроения, работающей при температуре до 300 °С, применяют марганцовожелезную латунь ЛЦ40МцЗЖ, содержащую 53—58% Си; 3— 4% Мп и 0,5—1,5% Ре. Ее механические свойства: ав = 392 МПа, 6 = 10%, НВ = 900 МПа.
В ряде случаев применяют обладающую хорошей жидкотекучестью кремнистую латунь ЛЦ16К4 (78—81% Си; 3,0—4,5% Э1).
Сплавы на основе свинца и олова. Легкоплавкие оловянные, свинцовые и оловянно-свинцово-сурмянистыс сплавы иногда применяют для изготовления деталей, не несущих больших нагрузок, но отличающихся высокой точностью размеров (шрифты в полиграфической промышленности, детали механизмов счетных машин и цифровых барабанов). Обычно эти сплавы содержат 4—18% ЭЬ и 1—33% РЬ. Они легко поддаются пайке мягким припоем.
Свинцовые сплавы имеют плотность около 10 000 кг/м3, ав = = 504-80 МПа и НВ = 1004-200 МПа. Низкая температура плавления этих сплавов, не превышающая 325 °С, обеспечивает простоту процесса и высокую стойкость пресс-форм. Специальные сплавы на основе свинца, применяющиеся в полиграфии, содержат 2—4% Эп, 20—30% ЭЬ и до 1% Си. Небольшая присадка меди задерживает рекристаллизацию свинца и способствует получению мелкозернистой структуры, что повышает коррозионную стойкость литых деталей. Разработаны свинцовые сплавы, не содержащие олова. В них входят 10—16% ЭЬ и 1—5% Аэ.
Черные сплавы. Литье под давлением чугуна не нашло применения. Литье под давлением стали применяют пока еще в небольших масштабах на специализированных участках и специальном
2.8. Механические свойства образцов из стали 10Х18Н9Л
(по данным В. М. Белова)
Вид образца |
°в< МПа |
в, % |
Из прутка диаметром 400 мм в отожженном состоянии, вырезанный вдоль волокна |
670 |
66 |
Из детали, отлитой под давлением |
550 |
52,3 |
Из детали, отлитой по выплавляемым моделям |
520 |
51 |
2.9. Механические свойства отливок из хромоиикелевой стали
Способ литья |
°в |
°о,а |
в, % |
МПа | |||
Под давле |
(750—820)/(820—860) |
(420—440)/(400—420) |
(20—38)/(35—55) |
нием 1 | |||
В песчаные |
770 |
370 |
55 |
формы |
\ |
1 В числителе — механические свойства отливок без термообработки, в знаменателе — после термообработки.
оборудовании с пресс-формами, изготовленными из молибденового сплава — единственного материала, обеспечивающего их достаточную работоспособность и стойкость. Экономическая целесообразность изготовления деталей литьем под давлением из сплавов с высокой температурой плавления взамен проката определяется снижением объема механической обработки. Из черных сплавов изготовляют те детали, масса которых играет решающую роль в работе изделий (транспортные и газотурбинные двигатели, судовая арматура, атомные энергетические установки, приборы оптической промышленности) [5].
Исследования показали, что наиболее подходящими для литья под давлением являются коррозионно-стойкие стали [6]. Они значительно дольше затвердевают, чем обычные низкоуглеродистые и низколегированные стали, имеют более низкую теплопроводность, благодаря чему повышаются четкость контуров отливки и качество ее поверхности. Углеродистые стали сложнее отливать под давлением из-за высокой температуры плавления, узкого интервала кристаллизации и большой усадки.
В СССР освоено литье под давлением сталей 10Х18Н9Л, 20Х13Л (ГОСТ 2176—77). Установлено, что чем ниже температура плавления стали и чем меньше твердость отливки при температуре выталкивания ее из пресс-формы, тем более пригодна сталь для литья под давлением. Средние значения механических свойств 10—15 образцов с диаметром 5 и длиной 50 мм в закаленном состоянии из стали 10X18H9JI, изготовленных различными способами, приведены в табл. 2.8.
По результатам лабораторных исследований фирмы General Electrik (США), детали из хромоникелевой стали (18%, Сг, 8% Ni), полученные литьем под давлением, обладают более высокой прочностью и коррозионной стойкостью, чем детали, полученные литьем в песчаные формы (табл. 2.9).
2.2. ОБЩИЕ ПРИНЦИПЫ КОНСТРУИРОВАНИЯ ЛИТОЙ ДЕТАЛИ
Основные преимущества литья под давлением (высокая производительность, точность размеров отливки и высокое качество поверхности) в полной мере могут быть реализованы в производстве только в том случае, если при конструировании литой детали учтены все особенности технологического процесса.
Под технологичностью литой детали подразумевают такое ее конструктивное оформление, которое, не снижая основных требований к конструкции, способствует получению заданных физико-механических свойств, размерной точности и шероховатости поверхности при минимальной трудоемкости изготовления и ограниченном использовании дефицитных материалов.
Конструирование литой детали основано на анализе факторов, характеризующих преимущества и недостатки технологического процесса литья под давлением по сравнению с другими способами литья. Чтобы полнее использовать возможности процесса литья под давлением, нужно уже на стадии конструирования литой детали учитывать все его особенности. Прежде всего, конструктора и технолога-литейщика должна связывать творческая работа. Это позволит создать конструкцию, не только отвечающую техническим требованиям при эксплуатации изделия, но получить отливку, отвечающую возможностям технологии литья под давлением при соблюдении экономической целесообразности ее получения на заданную программу выпуска. Высокая точность размеров, вызывающая необходимость иметь дорогостоящую оснастку, высокая производительность, требующая сложного оборудования, ограничение размеров и массы отливок, а также и повышенное содержание в них газов — все это требует создания оптимальных, экономически целесообразных и технически выполнимых конструкций.
При разработке чертежа литой детали необходимо в первую очередь установить, какие требования являются определяющими для данного изделия при его эксплуатации: прочность, герметичность, жесткость, качество поверхности, внешний вид или эстетическая форма.
Детали, предназначенные для изготовления литьем под давлением, в зависимости от конфигурации их наружных и внутренних поверхностей можно условно подразделить на четыре группы слож-
2.10. Группы сложности литых деталей
Группа слож ности і |
Характе- |
Характеристика поверхностей | ||
ристика деталей |
наружных |
внутренних |
деталей | |
і |
Простые |
Прямолинейные и гладкие, с невысокими ребрами, буртиками, бобышками, отверстиями |
Отсутствуют |
Крышки, фланцы, ручки, втулки, маховики |
п |
Слож ные |
Криволинейные и прямолинейные с несколькими пересекающимися плоскостями |
Сложные с двумя пересекающимися плоскостями или цилиндрическими участками |
Сложные корпуса приборов, корпуса двигателей мотоциклов, велосипедов, мотороллеров, насосов |
ні |
Особо слож ные |
Криволинейные и прямолинейные, пересекающиеся под углом, с выступающими частями и углублениями очень сложной конфигурации |
Сложные с криволинейными и прямолинейные с пересекающимися участками |
Блоки и головки блоков цилиндров автомобильных двигателей, сложные корпуса насосов |
ности (табл. 2.10). По назначению эти детали можно подразделить на три группы: прочные, герметичные и декоративные.
Для того чтобы обеспечить производство бездефектных отливок, необходимо, создавая чертеж литой детали, определить оптимальную плоскость разъема будущей пресс-формы и возможность формирования отверстий с помощью подвижных или неподвижных стержней. Литая деталь должна обладать конструкционной прочностью, жесткостью и герметичностью, быть технологичной. Рекомендации по конструктивному оформлению литой детали до последнего времени основываются на обобщении накопленного годами производственного опыта. Поскольку конструкции литых деталей и технологии их изготовления непрерывно совершенствуются, то эмпирические методы ограничивают возможности получения отливок оптимальной прочности, надежности, металлоемкости и долговечности.
Если в технологии уже имеются научные подходы к выбору оптимальных режимов процесса получения деталей, разрабатываются типовые проектные решения технологических процессов с применением ЭВМ и проводятся работы по созданию систем автоматизированного проектирования (САПР) литейной технологии (ЛТ), то при конструировании литой детали количествен-
2 Заказ 66 ншй метод еще только начинает разрабатываться. Основным этапом данного метода является машинный поиск оптимального варианта конструкции лнтой детали и технологии ее изготовления с использованием математических моделей статистического, экономико-математического и физико-математического характера [22]. Автоматизированное проектирование литой детали должно учитывать связи между ее конструкцией, механическими свойствами, наличием или отсутствием дефектов.
33
В современных условиях при достаточно обоснованных исходных данных для составления пакета программ автоматизированное проектирование литой детали может обеспечить выбор оптимальной конструкции.
Неже/70/77е/?ЬН6Ш
вариант
Желательный
вариант
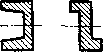
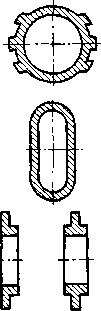
Рис. 2.1. Поперечные сечення лнтых деталей

■Зу|-~у\
Уже разработаны методологические основы конструирования элементов с целью получения научно обоснованных исходных данных для составления пакета программ САПР конструкций литых деталей [51, 60]. Конструкцию литой детали следует рассматривать как систему с последовательным и параллельным соединением ее конструктивных элементов, например различного рода сопряжений и сочленений стенок и узлов. Все эти элементы взаимосвязаны, но в процессе формирования отливки и ее свойств выполняют самостоятельные функции.
На конфигурацию литых деталей значительное влияние оказывают низкий модуль упругости, особенно магниевых сплавов, и их чувствительность к местным концентрациям напряжений. Чтобы избежать деформаций и трещин, вызванных этими свойствами, по возможности следует использовать двутавровые, швеллерные, зетовые, цилиндрические и другие поперечные сечения (рис. 2.1).
Габаритные размеры литой детали, а следовательно, и площадь проекции ограничивают минимальную толщину ее стенки при данном усилии запирания машины литья под давлением. На толщину стенки влияет жидкотекучесть сплава и технология, а
Рис. 2.2. Зависимость плотности и механических; свойств алюминиевых литых деталей от толщины их стеион
толщина стенки в свою очередь — на прочность и жесткость литой детали.
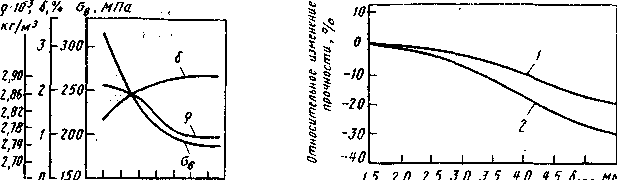
- д\-150 I I I I I [ I
1,5 г,0 2,5 5,0 3,5 5,0 5,5 6вт„,мм
0 1 2 3 5 5 6втл,нм
Рис. 2.3. Относительное изменение прочности литых деталей из цинковых {1) и алюминиевых (2) сплавов при увеличении толщины их стенок
В зависимости от толщины стенки изменяется плотность отливки и ее механические свойства. С уменьшением толщины стенки литых деталей (рис. 2.2), отлитых под давлением из сплава АЛ4, плотность р и временное сопротивление внзрастают, а относительное удлинение уменьшается. Увеличение прочностных свойств объясняется возрастанием роли гидродинамического уплотнения в тонкостенных отливках. Оптимальное сочетание механических свойств (огв = 250 МПа, 6 = 2%) наблюдается при толщине стенки 2,5—3 мм. Прочность литых деталей из цинковых сплавов при увеличении толщины стенки снижается не так значительно, как литых деталей из алюминиевых сплавов. На рис. 2.3 приведена зависимость относительного изменения прочности литой детали (в процентах по отношению к прочности литой детали толщиной 1,5 мм) при увеличении толщины ее стенки [113]. При увеличении толщины стенки от 1,5 до 5 мм прочность алюминиевых деталей падает на 30%, а деталей из цинкового сплава — лишь на 20%.
Конструкция литой детали и толщина ее стенки зависят от соотношения пределов прочности при сжатии и растяжении. По данным М. Шенберга, при сжатии для магниевых сплавов временное сопротивление разрыву в 1,5—2 раза превышает временное сопротивление разрыву при растяжении. Это обстоятельство необходимо учитывать при выборе конфигурации элементов детали, так как нетехнологичные конструкции подвергаются растягивающим напряжениям, а технологичные — сжимающим. (рис. 2.4).
Современные машины литья под давлением, развивающие в момент кристаллизации отливки высокие давления за короткий промежуток времени, позволяют изготовлять тонкостенные отливки с толщиной стенки 0,8—1,5 мм. Этому способствует разработка новых способов заполнения медленным сплошным потоком
е поеледующей эффективной подпрес-совкой через утолщенные питатели. Сочетание оптимальных тепловых условий затвердевания е подпреееовкой дает возможность получать литьем под давлением толстостенные отливки из эвтектических сплавов е широким интервалом кристаллизации: заэвтек-тических силуминов (17—19% 51),
термоупрочняемых сплавов системы А1—51—Си, магниевых сплавов, бронз и латуней.
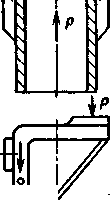
и
Щ
{;
Эксперименты, проведенные А. А. Гетьманом [22], позволили получить необходимые количественные данные для оценки эффективности технологического процесса изготовления литых ложеиная нагрузка) деталей. Показателями эффективности
в)
а)
Рис. 2.4. Нетехнологичная (а) и технологичная (б) конструкции литой детали (Р — при-
являются технологический коэффициент запаса прочности и коэффициент, учитывающий концентрацию напряжений, влияние размеров детали и состояние ее поверхности. Полученные данные по конструированию элементов литых деталей являются исходными параметрами для системы автоматизированного проектирования конструкций литых деталей из различных сплавов.
2.3. ПРОЕКТИРОВАНИЕ ТЕХНОЛОГИЧНОЙ ОТЛИВКИ
Качество отливок, в первую очередь, определяется технологичностью их конструкции и технологией изготовления. Требования к конструкции отливки и технологии ее получения непрерывно изменяются, что снижает эффективность эмпирического подхода к созданию технологичной конструкции отливки. Однако количественный подход с использованием математических моделей статистического, экономико-математического и физико-математического характера, который может служить главным научным инструментом поиска оптимальной конструкции отливки, не нашел широкого применения в промышленности. Отдельные исследования, проведенные за рубежом и в нашей стране, еще не дают возможности использовать ЭВМ для создания технологичных конструкций сложных отливок, получаемых литьем под давлением. Поэтому разработанные рекомендации по проектированию технологичной отливки основаны на накопленном производственном опыте, отдельных научных разработках и анализе факторов, характеризующих преимущества и недостатки литья под давлением по сравнению с другими методами получения металлических заготовок или деталей.
Разработка чертежа отливки начинается с определения технических требований к ней.
На чертеже отливки должно быть указано еледующее:
1) все внешние и внутренние уклоны;
1 Ш=4Ш1 |
и | |
2) поверхности, требующие последующей механической обработки;
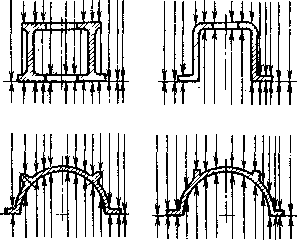
3) допуски на размеры;
4) участки поверхности, которые не должны иметь следов от выталкивателей, а также следов течения металла;
5) требования по герметичности и способы ее контроля;
6) виды защитных или декоративных покрытий;
7) участки, на которых не допускается пористость;
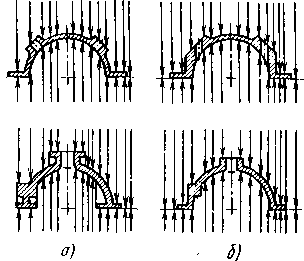
Рис. 2.5. Примеры конструкций отливок с теневыми участками (а) и без иих (б)
8) дополнительные требования для отливок, эксплуатируемых в необычных условиях (морская вода, кислоты, повышенная влажность, повышенная температура и т. д.);
9) марка сплава, ГОСТ или ТУ на сплав и масса отливки.
Точность отливок зависит прежде всего от точности изготовления пресс-формы и расположения плоскостей разъема.
Так как стоимость оснастки возрастает с увеличением требований к точности отливки,
то , отливку следует конструировать с учетом наиболее экономичного варианта изготовления пресс-формы. А экономичность ее изготовления зависит от положения плоскостей разъема. При конструировании отливки следует стремиться к созданию пресс-формы с одной плоскостью разъема. Для этого отливка не должна иметь внешних и внутренних поднутрений, препятствующих свободному удалению ее из пресс-формы. Возможность создания одной плоскости разъема определяют по правилу световых теней, по которому теневые участки при воображаемом освещении детали параллельными лучами в направлении, перпендикулярном плоскости разъема, должны отсутствовать (рис. 2.5).
Необходимо создавать отливки с прямыми линиями, прямыми углами и достаточно скругленными кромками в тех местах, где это практически осуществимо. Выемки и отверстия следует по возможности располагать перпендикулярно к плоскости разъема. Если отливка располагается в обеих полуформах, то для уменьшения усадочных напряжений внутренние стенки делают наклонными (рис. 2.6, а). При расположении отливки в неподвижной 1 и подвижной 2 полуформах (рис. 2.6, б) наибольшая поверхность стержня должна находиться в подвижной по-луформе. Боковое поднутрение 3 препятствует свободному удалению отливки из пресс-формы и должно образовываться боковым стержнем или подвижной щекой (рис. 2.6, в). Устранение этого поднутрения позволяет удалять отливку в направлении, перпендикулярном к плоскости разъема. Внутренние крепежные фланцы (рис. 2.6, г) с поднутрениями 4 можно вынести наружу в плоскость разъема, обеспечив свободный выход центрального стержня из полости отливки. Если конфигурация внутренней полости с поднутрением (рис. 2.6, д) не может быть изменена, то технологичная конструкция отливки предусматривает выемку 5 под фланец, заменяющей дно.
Нетехнологично
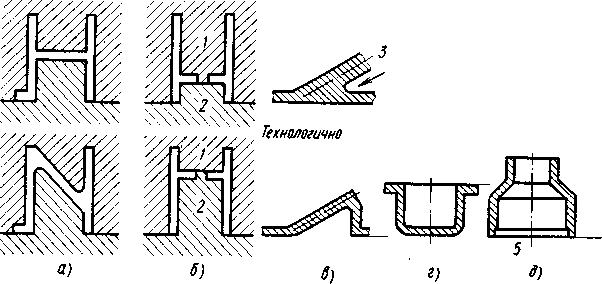
Рис. 2.6. Конструктивное оформление элементов с целью обеспечения их удаления из пресс-формы перпендикулярно плоскости равъема
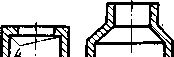
Нетехнологично
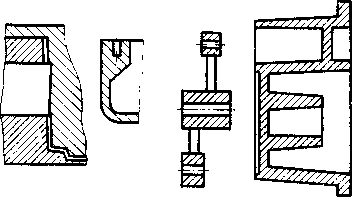
Технологично
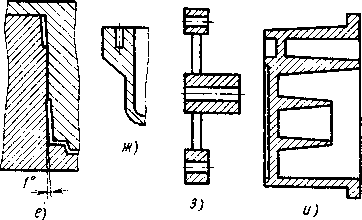
а
Рис. 2.7. Выбор плоскости разъема для цилиндрической симметричной (о) и иорпусиой (б) деталей (Я и Я — неподвижная и подвижная полуформы)
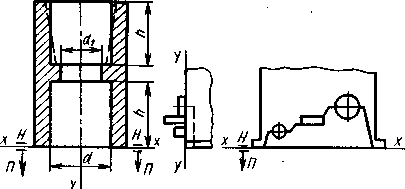
У
5)
В случаях больших отверстий, особенно на боковой стенке детали, требующих удаления стержней перед раскрытием формы, следует выполнять стенку литой детали таким образом, чтобы окно проходило по линии разъема формы (рис. 2.6, ё). Поднутрение, образованное в литой детали утолщением под крепежное отверстие (рис. 2.6, ою), нужно заменить утолщением на внешней стороне отливки с целью сохранения ее равностенности.
Конструкция отливки по возможности должна обеспечивать ее расположение в одной половине формы. Это повышает ее точность, сокращает стоимость формы. Если по конструктивным особенностям детали выполнить это требование невозможно, то желательно, чтобы отливка при раскрытии формы оставалась в подвижной половине. Ломаные линии разъема следует заменять прямыми (рис. 2.6, з). Глубокие полости по возможности следует располагать с одной стороны литой детали (рис. 2.6, и).
Следует стремиться к тому, чтобы число разъемов и стержней в пресс-форме было минимальным. Подвижные стержни, оформляющие отверстия или углубления в отливках, расположенные в плоскости разъема или наклонно к ней, заставляют увеличивать допуски на размеры и часто бывают причинами брака отливок по геометрии. Боковые стержни повышают трудоемкость изготовления пресс-формы и снижают производительность работы машины. Прямая плоскость разъема является наиболее предпочтительной, особенно при симметричном расположении рабочих полостей в многоместной пресс-форме. Однако стремление во чтобы то ни стало иметь одну плоскость разъема при проектировании сложных деталей может привести к потере технического и экономического эффекта литья под давлением. При конструировании отливки сложной конфигурации следует учитывать, что извлечение ее из пресс-формы не должно вызывать затруднений и что она должна оставаться в подвижной форме и удаляться выталкивающим механизмом. На рис. 2.7, а представлена отливка с симметричным расположением необрабатываемых полостей (диаметром й и высотой к) относительно средней перемычки с отверстием диаметром Если плоскость разъема будет проходить по

Рис. 2.8. Варианта размещения отливки П-образной колодки в пресс-форме (Я и Я — иеподвнжная и подвижная полуформы)
плоскости х—х, то, вследствие равномерности обжатия стержней, формирующих полости диаметром й, нет гарантии, что отливка при раскрытии пресс-формы останется в ее подвижной части. В этом случае следует увеличивать конусность одной из полостей (см. рис. 2.7, а, пунктирная линия). Если конструкция детали не допускает уклона или конусности, то плоскость разъема переносят на плоскость у—у. Однако такой перенос зйачительно удорожает пресс-форму и вызывает образование облоя на внешней цилиндрической поверхности отливки.
Конструкция детали должна обеспечивать такое размещение плоскостей разъемов, чтобы следы от этих плоскостей проходили по внешним углам отливки. Например, отливка, представленная на рис. 2.7, б, при расположении плоскости разъема по у—у потребует очень трудоемких операций по зачистке облоя и заусенцев. Перенесение разъема на плоскость х—х, несмотря на усложнение пресс-формы, снизит общую себестоимость отливки.
Чем проще конфигурация детали, тем больше вариантов ее расположения в пресс-форме. На рис. 2.8 приведены шесть вариантов выбора плоскости разъема для отливки П-образной колодки, в зависимости от которых изменяются величина уклонов на внешних поверхностях отливки и размерная точность отливки.
Проектируя отливку, следует предусматривать возможность соединения в одну нескольких деталей; это позволит упростить конструкцию и повысить жесткость изделия, уменьшить число обрабатываемых поверхностей, снизить трудоемкость изготовления и расход металла. Особенно эти преимущества проявляются при массовом и серийном производстве. Соединение нескольких деталей в одну служит показателем технологичности конструкции при условии, что это не намного усложняет и удорожает изготовление пресс-формы. На рис. 2.9 показана сложная отливка корпуса, образованного соединением в одно целое нескольких деталей. Высокая стоимость пресс-формы оправдывается при крупносерийном производстве.
В некоторых случаях, особенно при небольших производственных программах, выгодно разделить сложную отливку на несколько простых. При этом упрощается конструкция пресс-формы и уменьшается возможность появления брака. На возможность разделения отливки влияют особенности эксплуатации изделия, например замена быстроизнашивающихся деталей (рис. 2.10).
При проектировании отливки следует учитывать, что чем больше ее габаритные размеры, особенно за счет выступающих частей (рис. 2.11, а), тем сложнее и дороже пресс-форма. Поэтому следует стремиться к тому, чтобы отливка имела компактную конфигурацию и по возможности небольшие размеры (рис. 2.11, б.)
Толщина стенки отливки определяется совокупностью конструктив- Рис. 2.9. Корпус, образовавших и технологических факторов. ннй соединением нескольких К главным конструктивным факторам деталей относятся масса отливки, жесткость
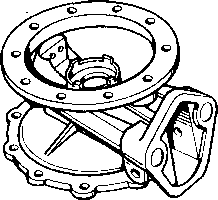
конструкции и требования к прочности и герметичности. Основными технологическими факторами являются возможность заполнения и подпрессовки отливки, выталкивания горячей отливки из пресс-формы и применения высокопроизводительного оборудования. При литье под давлением обеспечение направленности затвердевания отливки затрудняется высокими скоростями кристаллизации, поэтому следует создавать отливки, в которых металл затвердевал бы одновременно по всем сечениям. Этим условиям удовлетворяют только равностенные конструкции с минимально возможной толщиной стенки, позволяющие избавиться от концентрированных усадочных и газовых раковин. Направленность затвердевания отливок таких конструкций обеспечивается не толщиной стенки, а надлежащим расположением литниковой системы и каналов водяного охлаждения.
В деталях должны отсутствовать массивные места, отделенные друг от друга тонкими перегородками, поскольку в них не может быть обеспечена качественная подпрессовка. На рис. 2.12 приведены примеры ликвидации утолщенных мест, образующихся при сочленении или пересечении стенок литых конструкций. Если массивные места в отливке необходимы, то следует учитывать возможность их интенсивного охлаждения или локальной подпресбовки в пресс-форме.
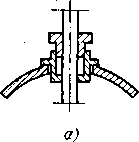
Рис. 2.10. Корпус сальника, отлитый отдельно (а) и вместе (б) с цилиндром
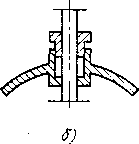
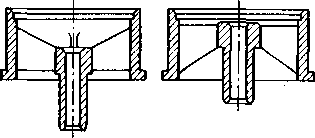
а) б)
Рис. 2.11, Нетехнологнчная (а) и технологичная (б) конструкции отливки
2.11. Зависимость минимально допустимой толщины стенки отливки от размера ее поверхности и типа сплава
Площадь внешней поверхностн отлнвкн, си1, прн толщине стенки, мм
Сплав
Более
500
25 — 100
До 25
250—500
100—250
Цинковый |
0,5 |
0,8 |
Алюминиевый |
0,8 |
1,2 |
Магниевый |
1,0 |
1,5 |
Медный |
2,0 |
2,5 |
Сталь |
2,0 |
3,0 |
1,0
1,5
2,0
3.0
5.0
1.5
2.5
2.5
3.5
2,0
3.0
3.0
Толщина сечений литых деталей зависит от прочностных и технологических свойств сплава. Значения минимально допустимой толщины стенки для различных сплавов в зависимости от площади внешней поверхности отливки приведены в табл. 2.11. На современных машинах, развивающих скорость прессования до 8 м/с, можно получать отливки с еще более тонкими стенками.
Если отливка имеет резкие переходы от толстых сечений к тонким, то в этих местах могут возникать горячие трещины. Чтобы этого не' происходило, необходимо создавать равностенные конструкции, предусматривать плавные переходы и радиусы закруглений между элементами литых деталей с разными сечениями рис. 2.13.
Конфигурация перехода зависит главным образом от соотношения толщин сопрягаемых элементов. При незначительной их
Рнс. 2.12. Разностенные (а) и равностенные (б) элементы отливок
Рнс. 2.13. Изменение конструкции отлнвкн с целью устранения массивного места:
а — нетехнологично; 6 — технологично
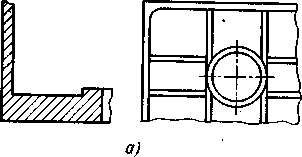
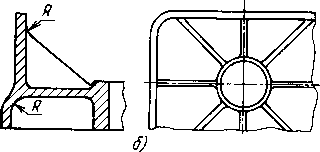
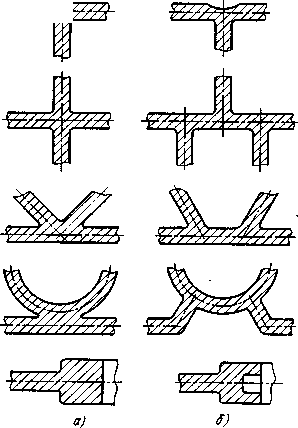
а) S) в) г) д)
Рве. 2.14. Переводя от толстый сечений И ТОНКИН
разнице (6jJ6a < 2) перехода рекомендуется осуществлять но радиуеу R = -г- (бх -f- б2), но не должна быть менее
1 мм (рис. 2.14, а).
Если 6j_/6a > 2, то следует применять так называемые клиновые сопряжения (рис. 2.14, б), в которых / 4k. Так как k =
= бх — 62, то I > 4 (бх — 62).
При перпендикулярном соединении стенок и отношении ®х/^2 1,75 (рис. 2.14, в) возможно сопряжение по радиусу
R = (бх + ба)/4.
При отношении бх/ба > 1,75 рекомендуется клиновое сопряжение, которое в зависимости от конструктивных требований выполняется с утолщением на тонкой (рис. 2.14, г) или на толстой стенке (рис. 2.14, д). При клиновом сопряжении перпендикулярных стенок /г = 3 УА — ба или k « (fix + Sa)/2, a 4k. Радиус внутренних закруглений должен быть не менее 0,8 мм, но не превышать толщину сопрягаемых стенок. Исследование зависимости механических свойств элементов отливок от их конструктивного оформления свидетельствует о том, что увеличение радиуса закругления во внутреннем углу сопряжения от 25 до 75% толщины ребра резко повышает долговечность конструктивных элементов толщиной 2 мм. Дальнейшее увеличение радиуса закругления лишь незначительно повышает долговечность. Это связано с тем, что при малых радиусах закругления повышается склонность узла сопряжения к образованию трещин, а с увеличением этого радиуса снижается плотность узла сопряжения вследствие ухудшения его питания через стенки малой толщины [22].
Принцип скругления переходов и углов не относится к поверхностям, которые пересекают плоскость разъема, где все грани должны оставаться прямоугольными и острыми (рис. 2.15). Эти грани могут быть скруглены на готовой отливке после удаления облоя. Если же острые грани при нормальном расположении плоскости разъема недопустимы, то необходим более сложный разъем пресс-формы.
Внутренний радиус закругления зависит от вида сплава. Для цинковых сплавов радиус может быть в 1,5 раза меньше, чем для алюминиевых сплавов. Особенно чувствительны к радиусу закругления магниевые сплавы, при кристаллизации которых в углах отливок наблюдается концентрация Напряжений, вызывающих горячие и Холодные трещийы. Холодные трещины возникают чаще всего в отливках, работающих при циклических нагрузках. Для таких отливок радиусы закруглений должны быть не менее половины толщины стенки.
Отверстия и окна в отливках, получаемых литьем под давлением, выполняют тремя способами: полностью литьем, частично литьем с последующей механической обработкой и полностью механической обработкой. Выбор способа зависит и пресс-формы, технологических возможностей процесса и масштаба производства. Для тонкостенных отливок небольших серий отверстия диаметром до 3 мм можно выполнять сверлением, в этом случае нет опасности отклонения режущего инструмента и вскрытия пор или раковин. В крупносерийном и массовом производстве выгоднее получать литые отверстия. В толстостенных отливках из цинковых сплавов отверстия диаметром до 1 мм, в отливках из алюминиевых и магниевых сплавов отверстия диаметром до 1,5 мм, в отливках из медных сплавов отверстия диаметром до 3 мм следует выполнять сверлением, ибо тонкие стержни быстро выходят из строя, а замена их в пресс-форме требует длительного времени. Остальные отверстия рекомендуется выполнять литьем, за исключением тех случаев, когда несколько отверстий близко расположены друг к другу и суммарная величина усилия охвата металлом стержней чрезмерно велика или же когда расстояние между отверстиями должно быть настолько точным, что колебания усадки металла и температурного расширения пресс-формы не обеспечивают требуемых допусков.
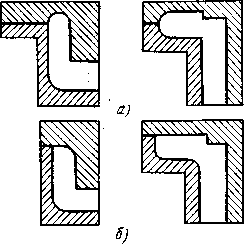
Рнс. 2.15. Выполнение закруглений н острых граней в плоскости разъема:
а — нетехнологнчио; б — технологично
от конструкции отливки
При конструировании отверстий (табл. 2.12) следует учитывать нецелесообразность применения длинных тонких стержней (рис. 2.16, а). Отверстия в боковой стенке (рис. 2.16, б) часто могут быть выполнены без стержней. Несколько боковых отверстий лучше располагать параллельно друг другу (рис. 2.16, в), чтобы использовать для движения стержней один механизм (клиновой или гидравлический). Боковая стенка е отверстием (рис. 2.16, г) должна отстоять от другой стенки минимум на 3 мм. Следует избегать расположения отверстий (стержней) в подвижной и неподвижной полуформах (рис. 2.16, д), лучше предусмотреть возможность последующей механической обработки. Если литое отверстие трудно выполнить, то оно может быть обо-
2.12. Допустимые размеры литых отверстий
Сплав |
Минимальней диаметр гі, мм |
Максимальная глубина отверстия |
Конусность, % длнны | ||
практически рекомен дуемый |
техноло гически ВОЗМОЖНЫЙ |
глу хого |
сквоз ного | ||
Цинковый |
1,5 |
1,0 |
ы |
ш |
0,2—0,5 |
Алюминиевый |
2,5 |
1,5 |
ы |
6<і |
0,5—1,0 |
Магниевый |
2,0 |
1,5 |
5 д. |
і од |
0,3—0,5 |
Медный |
3,0 |
2,5 |
Ы |
4 Л |
0,8—1,5 |
значено центром под сверло (рис. 2.16, е). Нельзя допускать пересечения отверстий, требующих пересечения стержней в пресс-форме (рис. 2.16, ж). При оформлении больших глухих отверстий дно (конец стержня) не должно иметь острых кромок (рис. 2.16, з). Толщина дна глухих отверстий должна быть минимальной, чтобы исключить действие чрезмерной усадки металла на стержень
Нетехнологично
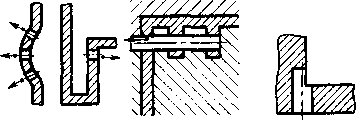
Технологично
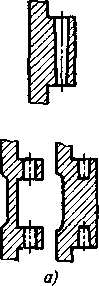
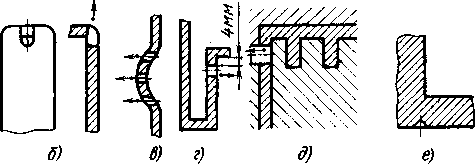
Нетехнологично
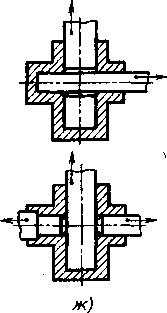
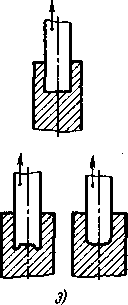
Технологично
к
и)
к)
Рис. 2.16. Конструирование литы* отверстий
(рие. 2.16, и). Иногда в целью устранения локальных утолщений рекомендуется делать технологичевкие отверстия или окна (рис. 2.16, к).
Отверстия и окна в отливках по возможности должны быть сквозными. Это позволит оформлять их е двух сторон, что исключит искривление
”1 |
г бр | ||
Ф 1 | |||
-л |
1 л |
/7 | |
-ШШ |
ШШ, | ||
°г |
Рис. 2.17. Ребро жесткости
стержней под воздействием высокого давления запрессовки и, следовательно, смещение центров отверстий.
Для сохранения конструктивной
прочности тонкостенных отливок применяют ребра жесткости. Они уп
рочняют стенку отливки, уменьшают ее прогиб под нагрузкой и препятствуют короблению. Рациональным конструкторским решением является распределение стыков ребер в шахматном порядке, позволяющее избежать скопления больших масс металла на пересечении нескольких профилей (см. рис. 2.12). Ребра должны иметь уклоны, по возможности равномерную толщину, закругленные внешние и внутренние края. В целях обеспечения равномерного уплотнения и охлаждения металла толщину ребер делают близкой к толщине стенки отливки. Рекомендуется следующее соотношение (рис. 2.17): бр = (0,8-г-0,9) ботл, где бр — средняя толщина ребра, бр = = 0,5 (бх + 62).
Высота Н ребра, в первую очередь, зависит от конфигурации детали. Однако не рекомендуется соотношение Лр> 10ботл. Внутренние радиусы Я назначают так же, как при любых пересечениях стенок. Радиус г скругления внешних кромок должен быть не менее 0,5 мм.
Высота ребер жесткости цилиндрических деталей обычно удовлетворяет условию Л > 41 (рис. 2.18, а). Во многих конструкциях, например в отливке плоской крышки (рис. 2.18, б), ребра жесткости наряду с упрочнением отливки улучшают запол-няемость пресс-формы. При литье магниевых сплавов ребра жесткости улучшают течение металла даже в том случае, когда с внутренней стороны плоских стенок они имеют высоту всего
А-А
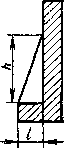
а)
Рис. 2.18. Ребра жесткости отливок 46
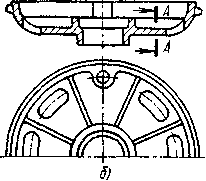
ЛИШЬ несколько деея- Нетехнологично Технологична
тых долей миллиметра.
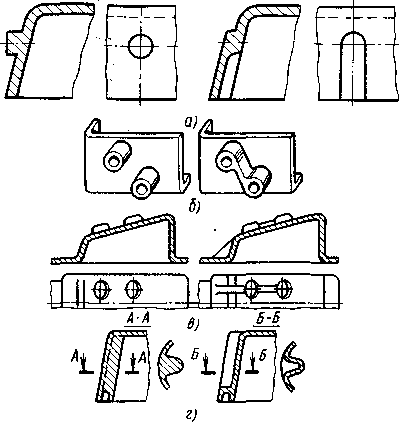
Рис. 2.19. Конструирование бобышки
При оформлении кромок отливок предусматривают ч опорные поверхности. Поскольку сплошные основания не позволяют получить опорную поверхность без коробления, их заменяют отдельными выступами, бортами или ножками, выполняющими функции ребер жесткости.
Бобышки и выступы, перпендикулярные к плоскости разъема, необходимо продлевать до этой плоскости или располагать на наружной стороне стенки, избегая поднутрений. Если оси бобышек расположены параллельно плоскости разъема, конструкция пресс-формы усложняется из-за дополнительных подвижных частей. Упростить конструкцию пресс-формы можно, несколько изменив конфигурацию отливки (рис. 2.19, а). Близко расположенные бобышки или выступы для лучшей передачи в них давления подпрессовки, а также для повышения жесткости отливки соединяют технологическими ребрами (рис. 2.19, б, в). Следует стремиться к устранению скопления металла в выступах и бобышках (рис. 2.19, г).
При кристаллизации металла возникают усадочные напряжения, препятствующие удалению отливки из пресс-формы. Для облегчения удаления отливки на поверхностях, перпендикулярных к плоскости разъема, предусматривают литейные уклоны. Особенно они важны на внутренних поверхностях, оформляемых стержнями.
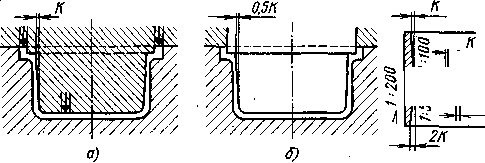
Рис. 2.20. Литейные уклоны
47